News
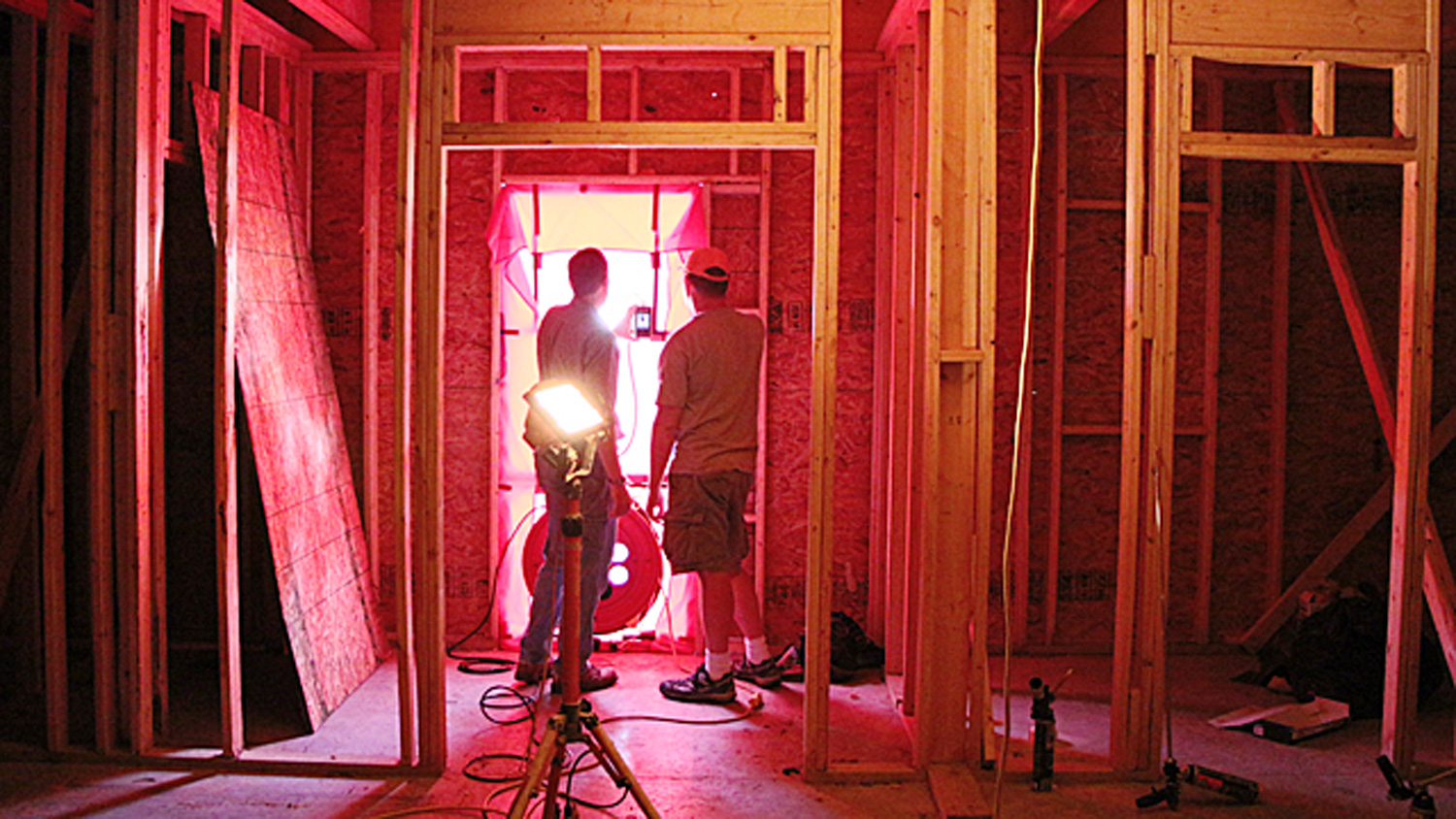
Is OSB Airtight?
Builders and researchers in North America and Europe report that air can leak right through oriented strand board
Most builders assume — and GBA has long reported — that oriented strand board (OSB) is a good air barrier. If a builder uses a high quality tape like Siga Wigluv, Zip System tape, or 3M All Weather flashing tape to seal sheathing seams, OSB wall and roof sheathing can act as a building’s primary air barrier. Energy consultant Marc Rosenbaum used the technique at two dormitory buildings at the College of the Atlantic in Maine and several projects on Martha’s Vineyard, and subsequently gave a presentation at a Vermont conference at which he advised builders who wanted low blower-door numbers to tape the seams of their OSB sheathing.
In recent months, however, many building experts have been surprised to read reports that some brands of OSB may not be airtight. The reported leakage isn’t coming from poorly taped OSB seams; instead, the air is allegedly leaking through the OSB panels themselves, even when the seams are flawlessly taped. While this type of air leakage sounds unlikely, evidence is accumulating that the reports must be taken seriously.
Among recent developments:
- An Irish engineer, Niall Crosson, has reported problems with two OSB-sheathed buildings that were too leaky to meet the Passivhaus airtightness standard.
- Architect Richard Pedranti and energy consultant Pete Vargo performed job-site testing in 2014 that convinced them that air was leaking through the Weyerhaeuser OSB installed on the walls of a Passivhaus project in Scranton, Pennsylvania.
- Three Belgian researchers — J. Langmans, R. Klein, and S. Roels — have published the results of laboratory tests showing that some European brands of OSB aren’t very airtight.
Defining acceptable air leakage
What’s the definition of an air barrier? In North America, some building codes have adopted the following definition: an “air barrier material” is defined as a material with a leakage rate of no more than 0.02 liters/sec-m² @75 Pa.
Building scientist Joseph Lstiburek helped develop this definition. “The .02 number was based on a suggestion from Gus Handegord,” Lstiburek told me. “He suggested that an air-barrier material should be defined relative to drywall. We tested drywall and the air leakage rate for drywall was a bit under .02. So that was the basis of the standard.”
The 2009 International Residential Code based its definition of “air-impermeable insulation” on the above definition of an “air barrier material.” The code defines an air-impermeable insulation is “an insulation having an air permeance equal to or less than 0.02 liters/sec-m² at 75 Pa pressure differential tested according to ASTM E 2178 or E 283.”
The National Building Code of Canada has also incorporated the above definition of an air-barrier material. (Once Canadian codes adopted this definition, DuPont, a major manufacturer of housewrap, was caught flat-footed. According to Lstiburek, Tyvek housewrap, widely promoted as an air barrier material, failed the Canadian standard. “They couldn’t sell Tyvek as an air infiltration barrier in Canada,” Lstiburek said. To address the problem, DuPont developed a new version of Tyvek for the Canadian market — one that was more airtight than the product they had been selling for years. Eventually, this product was branded as “Tyvek CommercialWrap” and was offered to U.S. as well as Canadian purchasers.)
A useful online document, “Air Permeance of Building Materials,” provides the results of laboratory testing in Canada of air leakage rates through a variety of materials. These lab tests showed that the following materials qualify as air-barrier materials: aluminum foil, EPDM roofing, plywood, XPS, particleboard, and gypsum wallboard. Asphalt felt (both #15 felt and #30 felt) fails the test, as do asphalt-impregnated fiberboard and EPS.
When I asked Lstiburek about air leakage through OSB, he told me that it was his understanding that “OSB has been easily able to meet the .02 requirement.” He added, “The Passivhaus airtightness standard of 0.6 ach50 is very difficult to achieve, but I would be surprised if the weak link [in a building envelope] is the air permeability of the OSB.”
In a follow-up phone call, Lstiburek elaborated. “OSB meets the North American definition of an air-impermeable material,” he said. “Anyway, that’s not where buildings leak.”
ASHRAE 90.1 includes an air barrier definition
Section 5.4.3.1.3 (“Acceptable Materials and Assemblies”) of ASHRAE 90.1, a model building code for commercial buildings, states that the following “continuous air barrier materials” are “acceptable”: “Materials that have an air permeance not exceeding 0.004 cfm/ft2 under a pressure differential of 0.3 in. w.g. (1.57 psf) (0.02 L/s.m2 @ 75 Pa) when tested in accordance with ASTM E 2178.” In other words, this definition is in alignment with the definition in Canada’s National Building Code.
This section of ASHRAE 90.1 goes on to state that “Oriented strand board — minimum 3/8 in.” is one of several materials that “meet the requirements of 5.4.3.1.3.”
According to Sam Glass, a research scientist as the U.S.D.A. Forest Products Laboratory in Madison, Wisconsin, the ASHRAE 90.1 stipulation is based on laboratory measurements of air leakage through three types of North American OSB. The measurements were made by Canadian researchers whose findings were published in a 2006 paper titled “A Thermal and Moisture Transport Property Database for Common Building and Insulating Materials.”
The Canadian researchers tested three types of OSB (3/8 inch, 7/16 inch, and 1/2 inch). Unfortunately, the brands of the OSB were not identified. All measurements of air leakage through these OSB samples were below the 0.2 liters/sec•m² @75 Pa threshold for air barrier materials.
Testing OSB with the job-site “balloon test”
Builders who are worried about air leakage through OSB panels have developed a simple job-site test to demonstrate the problem. A rectangle of polyethylene (measuring about 3 feet by 3 feet) is temporarily taped to the center of a panel of OSB wall sheathing (on the exterior side of the wall). The entire perimeter of the polyethylene is carefully taped to the OSB with a high-quality tape like Siga Wigluv.
Then a blower door is used to pressurize the house to 50 Pascals. If the polyethylene balloons out, that’s a sign that air is leaking through the OSB.
A report from Ireland
Niall Crosson, senior technical engineer at Ecological Building Systems in Dublin, Ireland, posted a report about leakage through OSB sheathing on a LinkedIn Web forum: “I’ve been on two sites in the last two months aiming for Passive House airtightness. One had 12.5 mm [1/2 inch] OSB and the other 18 mm [3/4 inch]. We struggled to get to the required N50 [airtightness goal of 0.6 ach @50 Pa] even though I couldn’t fault the application.”
Crosson continued, “I suggested to tape an air barrier membrane over a portion of the OSB.” In other words, the Irish builders decided to perform the balloon test.
“In both cases it blew up!” Crosson reported. “We then sealed the OSB fully [with a taped Pro Clima membrane called DA] and this made a dramatic improvement.”
For more information, see the PowerPoint slides from a Crosson’s presentation on this topic: Airtightness: When it’s not as airtight as it’s cracked up to be!
A report from Pennsylvania
Richard Pedranti is an architect in Milford, Pennsylvania. Pedranti recently sent me an e-mail describing his headaches with Weyerhaeuser OSB.
“The project where we experienced OSB air leakage is a new residence that my office designed to meet the Passive House standard,” Pedranti wrote. “The project started construction in June of 2014 and is located in Scranton, Pennsylvania. It’s my first Passive House project, and I was concerned above all else about reaching the aggressive airtightness requirement of 0.6 ach @50 Pa. … Our team spent a great deal of time making sure the construction was tight and sealed. The OSB is taped on the outside with Siga Wigluv. The top floor is a flat ceiling with the OSB fastened to the bottom of the roof trusses and then taped with Siga Wigluv. The contractor took it upon himself to foam every interior stud and plate. … The polyethylene vapor barrier [was] wrapped up from beneath the concrete slab and taped to the OSB with Siga Wigluv.”
So far, so good. Pedranti explained in an e-mail, “After starting the blower door and spending several hours sealing small leaks, it became clear to me the we were not going to get close to 0.6 ach @50 Pa. The lowest we measured was 1.1 ach @50 Pa.”
I telephoned Pedranti for more details, and he explained, “We had been pretty confident that we were going to pass the blower-door test with flying colors. We got the blower door in, and we started at over 1.5 ach50 early in the day. We were in there for 4 or 5 hours with a fog machine. We were using flashlights, tape, and foam, finding every leak we could. The consultants and contractors were all working hard and sweating. After a few of hours, we were reaching the point of diminishing returns. It was becoming clear that we weren’t going to get below 1 ach50. We were done.”
When the house was pressurized, the poly billowed out
“We were all quite frustrated at that point, and our building performance consultant, Pete Vargo, suggested doing a positive pressure test and looking around outside,” Pedranti wrote in his e-mail. “We reversed the fan and Pete said, ‘Let’s do a balloon test on the OSB just for fun.’ We taped a piece of polyethylene over a portion of the OSB and taped it with Siga Wigluv. The polyethylene immediately ballooned up just like the shroud of the blower door, and Pete declared that we have leaky OSB.”
Pedranti explained over the phone, “I wasn’t very excited to do this balloon test. I didn’t think it was true that the OSB was leaking. I thought it had to be the tape seams or the sill seal at the plate. We taped the poly up there and cranked the fan up, and it just happened instantaneously. We said, ‘This is unbelievable. How did we end up with this leaky OSB?’ I was quite upset.”
A photo of the test (shown at the top of this page) is a bit hard to interpret; according the Pedranti, this photo shows the second of two tests. The first test (using the large rectangle of polyethylene) was performed over a section of sheathing that included taped seams. The photo shows the second test; for this test, the polyethylene was slit horizontally below the OSB seam, and the lower rectangle of OSB was sealed with a new horizontal piece of Siga Wigluv tape to the OSB. For the second test, the tested area did not include any OSB seams.
“Bummer”
After observing these tests, Pedranti started asking questions. “When I returned to my office, I e-mailed a number of Passive House colleagues including Adam Cohen, Mike Kernagis, Dan Whitmore, and Chris Corson. They all had the same reaction: ‘Bummer — I’ve heard of this happening before.’ Dan suggested several liquid-applied solutions including Dow Corning Defendair 200, BASF Enershield, Prosoco Cat-5, and elastomeric paints.”
Solving the problem by painting the OSB with elastomeric paint wouldn’t be as easy as it sounds. “One limitation to our solution is that we did not want to remove the Siga Wigluv, which is a water-based tape,” Pedranti wrote. “After a cost and labor analysis, we opted for Siga Majpell [a European air barrier membrane that installs like housewrap] applied over the OSB with Siga Twinet. Twinet is a double-face adhesive tape. The Siga Majpell was also applied to the second floor ceiling.”
In our phone conversation, Pedranti said, “It cost $3,000 to fix the problem, and the contractor didn’t charge that much for labor. The double-sided tape is expensive.” After the new air-barrier membrane was installed over the OSB, a blower-door test showed an air leakage rate of 0.34 ach50 — well below the Passivhaus target of 0.6 ach50.
Pedranti will never again use Weyerhaeuser OSB. “I have changed the sheathing specification in future Passive House projects to Zip sheathing to avoid this issue.”
After hearing Pedranti’s story, I spoke with Alex Kuchar, Weyerhaeuser’s OSB technical manager, and asked him whether Weyerhaeuser has tested the airtightness of their OSB. “No, we have not,” Kuchar responded.
Testing in Belgium
An interesting paper on the issue of OSB airtightness was published by three Belgian researchers, J. Langmans, R. Klein, S. Roels. Their paper is titled “Air permeability requirements for air barrier materials in passive houses — Comparison of the air permeability of eight commercial brands of OSB.”
The Belgian researchers wrote, “Based on the recent cases where the OSB was too air-permeable to achieve an n-value [blower-door test result] lower than 0.6 ACH [at 50 Pa], discussion arose whether OSB is a suitable material for air barrier systems in passive houses.”
The three researchers decided to test OSB samples for air leakage. “Eight commercial brands of OSB from the major West European manufacturers were selected. The panels investigated are produced in Ireland, United Kingdom, France, Germany, Belgium or Luxembourg. … The thickness of OSB tested is 18 mm [3/4 inch] which is commonly used for timber framed [stick-built] constructions.”
Only one of the tested brands of OSB met the Canadian standard for an air-barrier material; the other seven tested brands were too leaky to pass the standard (see the graph in Image #9, below). The researchers wrote, “The results … clearly indicate a large difference between the air permeance of the different OSB brands tested. For example, OSB B is at least ten times more airtight then OSB A. Furthermore, although only three specimens were measured for each brand, a large variation is noticed within the same brand.”
The leakiest tested brand of OSB — designated “brand A” by the researchers — had an air leakage rate that was more than 10 times higher than the Canadian standard for an air-barrier material.
The researchers decried the lack of air leakage data on OSB: “Information of the air permeance of materials applied for air barrier systems is relatively rare. In Canada on the other hand, where the National Building Code (NBC) imposes an upper limit of 0.00096 m³/m²/h/Pa [0.02 liters/sec-m² @75 Pa] for materials composing the air barrier system, building materials’ [air] permeabilities are better documented.”
The researchers noted that the leakiest OSB samples were so leaky that it would be difficult for an OSB-sheathed house to meet the Passivhaus standard, even if every seam were perfectly sealed. This conclusion was based on a few assumptions and calculations. They proposed a few typical values for surface-to-volume ratios for Passivhaus buildings, and used these values in their calculations. They also noted that it’s logical to assume that some — probably most — of the air leakage through a tested building envelope will occur in locations other than through the OSB sheathing (since some leakage inevitably occurs through windows, penetrations, and difficult-to-seal cracks).
They wrote, “Assuming that the buffer necessary for unforeseen leakages [for example, leaks at penetrations and seams that are difficult to seal] should be at least 0.5 ACH as mentioned above, the air leakage through the air barrier material [i.e., the OSB] must be lower than 0.1 ACH … [in order to meet] the Passive House Standard. Based on the worst scenario used above, corresponding with a compactness of 0.91 m (A [OSB] /V =1.1), the upper limit for the air permeance results in 0.0018 m³/m²/h/Pa [0.037 liters/sec-m² @75 Pa]. This proposed limit is still less severe than the Canadian requirement [0.02 liters/sec-m² @75 Pa].”
Recommendations to builders
North American OSB manufacturers do not currently report the results of air leakage testing of their OSB.
There is no reason to believe that Weyerhaeser OSB is any more or less leaky than most other brands of North American OSB. In the absence of good testing data, it’s hard to choose among available brands of OSB.
It’s worth emphasizing that Weyerhaeser OSB is not defective. North American OSB is not marketed as an air barrier material, and current manufacturing standards for OSB do not require OSB to resist air leakage.
If the range of OSB performance among North Americian brands is similar to the range of OSB performance in Europe, it’s possible that some brands of North American OSB are as leaky as the Weyerhaeuser product that plagued Richard Pedranti, while other brands (as Joseph Lstiburek and Sam Glass report) are tight enough to meet the code definition of an air barrier material.
In the absence of data from manufacturers, however, builders are forced to make decisions based on the best available information and the anecdotes of their colleagues. At this time, builders who want to use OSB sheathing as an air barrier should probably avoid OSB manufactured by Weyerhaeuser and should instead specify Huber Zip sheathing. (Huber Zip sheathing is a brand of coated OSB; many builders have reported good success using taped Zip sheathing as an air barrier.)
A second way to address this issue is to specify plywood sheathing rather than OSB sheathing.
A third approach is to create an air barrier using different materials — for example, a taped European air-barrier membrane like Solitex Mento, Intesana, Pro Clima DA, or Siga Majvest; or a liquid-applied air barrier like StoGuard, Grace Perm-A-Barrier VP, Henry Company’s Air Bloc 31, DuPont Fluid Applied WB System, or Tremco Enviro-Dri.
Is the 50 pascal depressurization test relevant?
It would be interesting to know how often the stack effect and wind speeds are powerful enough to cause enough air leakage through OSB sheathing to matter very much.
I discussed this question with Vladimir Kochkin, the division director at Home Innovation Research Labs (formerly known as the NAHB Research Center). Kochkin pointed out, “This becomes a question of conversion of air leakage at 50 Pa to air leakage at natural pressures. Even if the OSB is leaking during the test, it does not mean it will leak substantially under natural pressures.”
Fifty Pascals of depressurization is roughly equivalent to subjecting a house to a 20 mph wind. While buildings regularly experience such winds, there are few locations in the world where such a high wind speed occurs very often.”
I went with Advantech 5/8″ on my latest Passive House build after hearing all of the complaints about OSB being an air leaking source. Of course, I went with a belt a suspenders approach too with Delta Vent SA + Siga interior membrane. Overkill in my opinon, but incredible how that OSB balloon expanded with the pressure test! Cheer, Brian @ https://materialsmagazine.com I write about my own building science adventures from time to time. Currently the marketer @ Alpen windows.
Same problem here in UK in 2021. leakage test on the OSB made the Intello membrane balloon out. Architect had not specified that the airtightness layer osb should actually be airtight. Building was a chalet bungalow with loads of pitched roof area. Covering the roof with 200mm wood fibre and Proclima Solitex Plus membrane, all joints and edges taped with Tescon Vana. Internal block walls no longer showing billowing Intello membrane, as now covered in 200mm EPS external wall insulation plus 20mm render. Last test April 2022 achieved 1.81 ach-1.