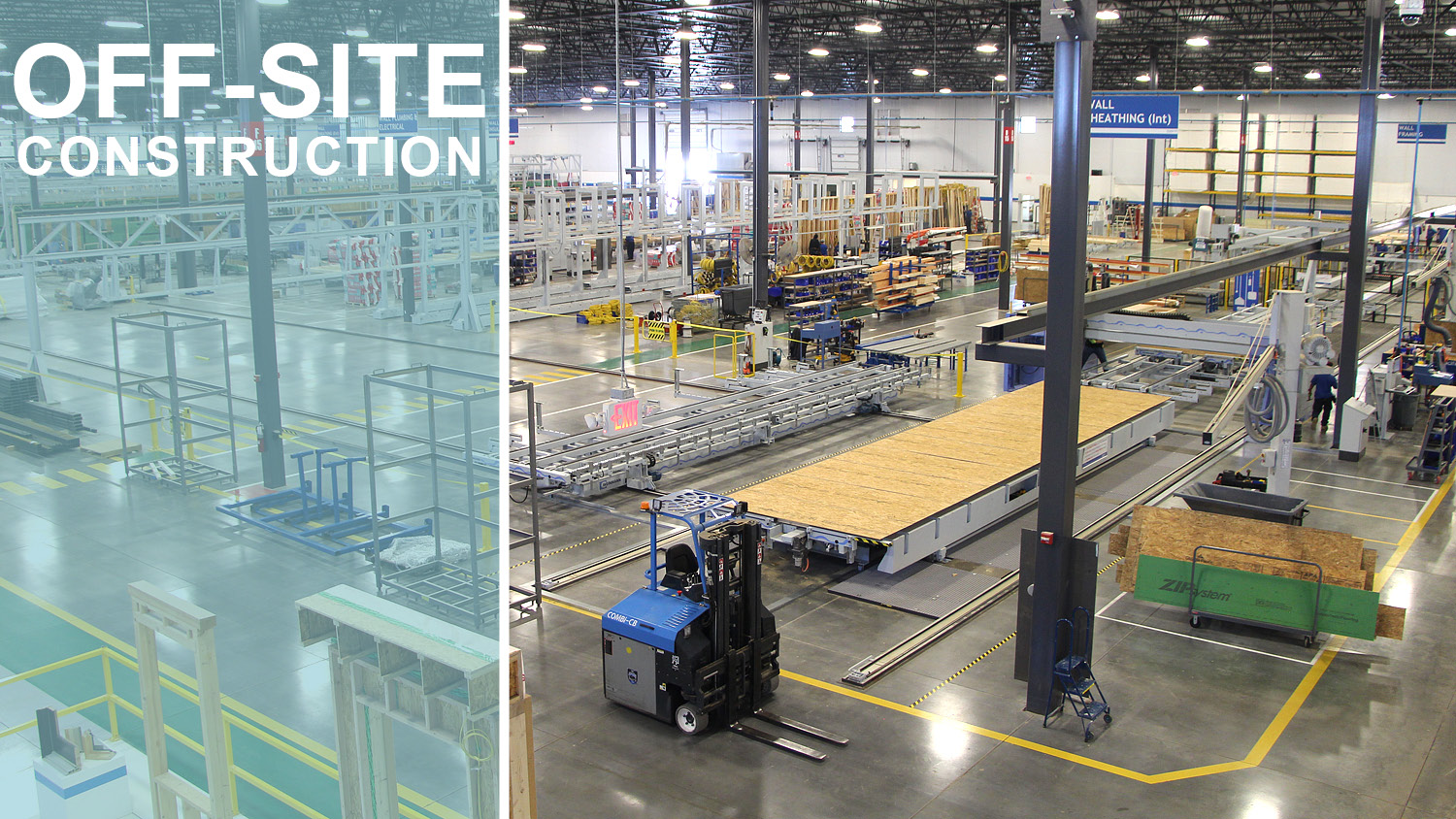
WHAT IS OFF-SITE CONSTRUCTION
Off-site Construction refers to the planning, design, fabrication, and assembly of building elements at a location other than their final installed location to support the rapid and efficient construction of a permanent structure. Such building elements may be prefabricated in a different location and transported to the site or prefabricated on the construction site and then transported to their final location. Offsite construction is characterized by an integrated planning and supply chain optimization strategy. Offsite manufacturing (OSM), offsite production (OSP) and offsite fabrication (OSF) are used when referring primarily to the factory work proper.
PLANT PREFAB
RPA LIVINGHOMES
From press release dated January 26, 2021
“Plant is focused on building homes that are as healthy and sustainable as possible and we push the boundaries," explains Plant Prefab Founder and CEO Steve Glenn. "We use the U.S. Green Building Council’s LEED for Homes program as well as our own stringent health and sustainability program, Z6, to create some of the world's healthiest homes with the lowest possible impact on the planet. Passive House is another major environmental certification program and it integrates uncompromising standards for occupant health, comfort, and energy performance. We are honored to be partnering with one of the nation's foremost Passive House experts and most experienced Passive House designers to introduce our first Passive House LivingHomes.”
Ranging in size from 2,218 to 3,182 square feet and from three to four bedrooms, RPA LivingHomes feature timeless modern design complemented by advanced building science. RPA LivingHomes 1 and 2 feature pitched roofs—optimized for photovoltaic panels—that create cozy living spaces, and all of the RPA LivingHomes offer open-plan living areas with large, expressive windows. RPA LivingHome 3 is distinctly Californian in design, inspired by mid-century case study homes.
Construction of all LivingHomes is made significantly more efficient with use of the Plant Building System (PBS), Plant Prefab’s patented, hybrid system for building prefabricated homes. PBS uses a combination of Plant Modules and Plant Panels, a new panelized construction system developed by Plant Prefab, which include plumbing, electrical, and finish materials. By integrating both modules and panels, PBS provides architects with greater design flexibility and reduces the complexity and cost of transportation and installation. Additionally, Plant Prefab’s PBS Design Guidelines provide best practices for architects on how to create home designs that are optimized for the most efficient production at Plant Prefab. The RPA LivingHomes are now available for customization on plantprefab.com/models, with pricing from $586,257 inclusive of all finishes, fixtures, appliances, and smart home technology. Site work and soft costs are additional.
ABOUT PLANT PREFAB With a mission to build a better world by design, Plant Prefab makes it faster and more efficient to build custom, high-quality, healthy, single-family and multi-family homes. Plant Prefab is the first Certified B Corporation™ prefabricated design and construction company dedicated to sustainable building, materials, processes, and operations.
RPA Livinghomes on Plant Prefab website
RPA LIVINGHOMES 1, 2, & 3
Visit RPA LivingHome 1
Visit RPA LivingHome 2
Visit RPA LivingHome 3
The Lang/St. Marie Residence is a prefabricated, Net Zero home in the New Jersey shore town of Spring Lake Heights designed as weekend retreat for retired couple from Brooklyn, New York.
The front of the modern Lang/St. Marie Residence blends into its well-established beach neighborhood in scale and appearance. The rear of the home is a fresh turn on modern living. A stunning 16-foot cantilever cuts strong horizontal lines across the landscape and creates a large covered outdoor space.
Landscape architect, Marsha Lea, joined the project to create a breathtaking garden space as a backyard retreat. The relationship with the outdoors was of the utmost importance to the homeowners. A 10ft high by 25ft wide retractable glass wall unifies the rear of the home and the backyard. This feature invokes a strong connection to nature and enables true indoor/outdoor beach living. With the lines between interior and exterior blurred, the home achieves a harmonious flow between the states.
Passive House design principles were employed in the design of the Lang/St. Marie Residence, resulting in low energy consumption for heating and cooling and a cozy, healthy indoor environment. The high performance triple pane windows allow for large expanses of glass and with the addition of a roof mounted PV solar system the home has achieved Net-Zero Building (NZB).
This custom home was translated from the architect’s building information modeling software into the machine language understood by robotic manufacturing systems. Using those instructions, the machines at the manufacturing facility created panelized wall assemblies for the home that were then transported from Maryland to New Jersey and assembled at the job site.
LANG / ST. MARIE RESIDENCE PHOTOS
The aesthetic, application of building science, and off-site fabrication combine to make the Lang/St. Marie Residence the epitome of modern residential design.
The Lang/St. Marie Residence was built using Passive House principles and building science strategies that create a comfortable, affordable, sustainable home with low energy consumption for heating and cooling.
Sustainable building principles include higher levels of insulation, airtight construction, triple-pane windows, the use of a heat recovery ventilator and passive solar orientation of the home on the building lot. These strategies allow the home to remain comfortable year-round without having a traditional HVAC system. This home requires less than half of the energy needed to heat and cool a typical American home yet feels more comfortable as drafts are eliminated and a stable temperature and fresh air quality is maintained throughout.
The unique combination of Passive House wall structures manufactured off-site illustrates what is possible in rapid and efficient creation of sustainable custom-designed homes. It allows for greater specialization than other prefab construction techniques, uses high-grade building materials and advanced manufacturing technologies in a controlled factory environment to create homes that expressly meet customer needs while saving both time and money.
Homeowner, Theresa Lang, says: “The architect’s work with us from the very start was both creative and collaborative. They took our wish list and transformed it into a beautiful design through a shared belief that functional passive house principles are consistent with a minimalist modern aesthetic.”
With improvements in technology and growing excitement from the architecture community, it has become apparent that modern building science and beautiful design are not mutually exclusive. This bodes well for promoting sustainable principles and innovative building strategies to wider audiences and implementing them into a larger share of new and renovated residential design.
LANG / ST. MARIE RESIDENCE CONSTRUCTION PHOTOS
Homeowner Elizabeth Scott worked with RPA to customize her own version of the firm’s existing line of prefabricated Passive House designs. This provided the confidence of a proven building system with a design that met her own specifications and needs.
The project is a continuation of a familial legacy in sustainable living for Scott. A jewelry artist, Scott grew up in a “post and beam passive solar house” that her parents built in 1979 with legendary builder Bruce Brownell, a pioneer in low energy residential design. Her Passive House is assembled on an 8.7-acre lot adjacent to the 23-acre lot where her parent’s home still sits.
Passive House takes advantage of super-insulated walls, internal heat gains and the sun shining through well-situated windows to produce the highest level of interior comfort available in a building today. Regardless of the weather outside in Scott’s town in upstate New York, this approach to home building reduces energy consumption by 80 to 90 percent compared to conventional homes.
Scott’s original plan involved building a small, 800 square foot Passive House along with a detached building to be used as her workspace. The prefabricated model featured two bedrooms and two bathrooms, but Elizabeth desired more living space in addition to the workshop. After consulting with the architect, she decided that a larger (2,125 square foot) model was more practical and a better investment.
To expand design options and cost-effectively increase living space, the team decided to add a Passive Roof assembly to Elizabeth’s home. The roof employs the same healthy, high performance materials as the Passive Walls and reclaims living space typically dedicated to the attic. Elizabeth’s customized Passive House is one and a half stories and features four bathrooms and three bedrooms.
SCOTT RESIDENCE PHOTOS
Spending her childhood in a home that took advantage of solar gains using a wall of windows and twice as much insulation as a typical home, Elizabeth always knew that she would one day build an energy efficient home of her own.
She learned about the Passive House standard and originally planned on building in 2009, but after realizing there were limited options available in the United States decided to wait until building alternatives improved.
“After growing up in my parent’s passive solar house, I always felt that it was too bad that the passive solar building technology did not develop further in the United States, until recently,” says Scott. “I was ecstatic to find this line of prefabricated Passive Houses employed 21st century building technology and quality materials, like foam-free, dense packed cellulose insulation. I was even more convinced that it had been worth my wait when I began working with my architect to customize the design of my home.”
Elizabeth worked with the architect over a six-week period to customize her home. From there, computerized building models automatically provided instructions to the manufacturer’s saw and production line where the panelized wall and roof components were created, a four to six-week process.
Once fabricated, the panels were shipped to the site, which had been prepared for assembly. Upon delivery, the design team and construction crew worked with local building partners to assemble Scott’s Passive House – a two-week process.
After setting the panels and installing the roof for a weather and air-tight fit, blower door tests were performed to ensure that the building met the rigorous Passive House air tightness standard. The home was then ready for the local builder partner to take over, installing the mechanical, electrical, plumbing, and interior/exterior finishes.
SCOTT RESIDENCE CONSTRUCTION PHOTOS
CASE STUDY: CHOI RESIDENCE
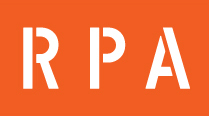
CONTACT US FOR MORE INFORMATION TODAY
Richard Pedranti
richard@richardpedranti.com
Office (570) 296-0466
Mobile (267) 294-9818