STORY
DESCRIPTION
The Scott Passive House was designed by a Pennsylvania-based architecture firm focused on energy efficient design and fabricated by an off-site construction firm in Maine that manufactures, delivers and assembles high-performance buildings. Homeowner Elizabeth Scott worked with the architect to customize her own version of the firm’s existing line of prefabricated Passive House designs. This provided the confidence of a proven building system with a design that met her own specifications and needs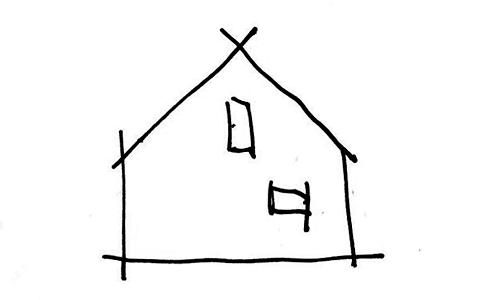
DESIGN
Spending her childhood in a home that took advantage of solar gains using a wall of windows and twice as much insulation as a typical home, Elizabeth always knew that she would one day build an energy efficient home of her own. She learned about the Passive House standard and originally planned on building in 2009, but after realizing there were limited options available in the United States decided to wait until building alternatives improved. “After growing up in my parent’s passive solar house, I always felt that it was too bad that the passive solar building technology did not develop further in the United States, until recently,” says Scott. “I was ecstatic to find this line of prefabricated Passive Houses employed 21st century building technology and quality materials, like foam-free, dense packed cellulose insulation. I was even more convinced that it had been worth my wait when I began working with my architect to customize the design of my home.” Elizabeth worked with the architect over a six-week period to customize her home. From there, computerized building models automatically provided instructions to the manufacturer’s saw and production line where the panelized wall and roof components were created, a four to six-week process. Once fabricated, the panels were shipped to the site, which had been prepared for assembly. Upon delivery, the design team and construction crew worked with local building partners to assemble Scott’s Passive House – a two-week process. After setting the panels and installing the roof for a weather and air-tight fit, blower door tests were performed to ensure that the building met the rigorous Passive House air tightness standard. The home was then ready for the local builder partner to take over, installing the mechanical, electrical, plumbing, and interior/exterior finishes.
DETAILS
MORE